HORIZONTAL DIRECTIONAL BORING 101
Referred to by many names, horizontal directional boring, horizontal directional drilling, trenchless excavation, underground drilling, and directional drilling, it's all the same thing, but to keep it simple, we’ll refer to it as Directional Boring. ​
Directional boring contractors use this method to place pipes or conduits underground with a machine that drills a pilot hole, then hitches up to whatever the desired conduit is to be installed, then pulls it back through the pilot hole, all without cutting an open trench from above.

TO DIG OR NOT TO DIG, THAT IS THE QUESTION
Traditionally open cut trenching is where an excavator, machine trencher or common hand tools, like a shovel, are used to open the soil to the desired width and depth to accept the pipe or conduit that is to be installed.
"Open Cut" is the preferred method dating back to 43 AD when the Romans invaded England.
They installed lead piping to route water from Aqueducts to public fountains and baths.
Today, open-cut trenching is still a great option unless there are too many obstacles to deal with.
These include:
​
-
Above-ground restoration is too costly
-
The excavated area cannot be shutdown
-
There are too many utilities to avoid
-
There is limited space for conduit or pipe
-
The job is time sensitive
-
All of the above
That is when Directional Boring is the obvious choice.
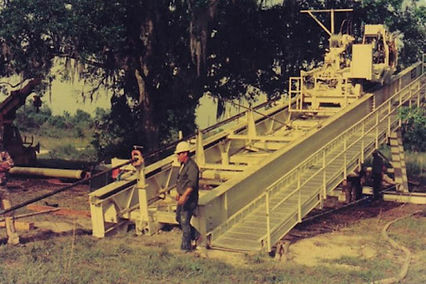
Martin Cherrington in the 1960s came up with the idea of Directional Boring.
With his experience and observations in gas line installation, he came up with a better and more efficient way to install conduit using a carriage-type machine that could drive pipe into the ground.
Today manufacturers and Directional boring contractors like Ditch Witch and Vermeer have taken Martin's methods to the stratosphere with Underground technology advancements.
Whether you're installing underground utilities such as water, sewer, gas, electric telephone and fiber optic etc., directional drilling is the preferred method and although commercial applications have dominated, residential needs are in high demand.
FREQUENTLY ASKED QUESTIONS
Here are answers to the most popular horizontal boring or directional drilling questions we receive from clients before proceeding with their utility or other projects.
1. What is horizontal boring used for?
Horizontal boring is primarily used as a method of underground drilling to install service pipes and conduits whilst minimally damaging or disturbing the area above ground.
​
2. How far can you bore horizontally?
Boring technology allows you to effectively bore up to approximately 8,000 linear feet with pipe diameters of up to 48 inches.
​
3. What is the difference between horizontal boring and directional drilling?
These two names are interchangeable and ultimately refer to and mean the same thing.
4. How accurate is directional boring?
Horizontal boring is extremely accurate and is not affected by magnetic fields from cables or railways, and is accurate up to 0.01° in pitch and 0.04° in azimuth.
​
5. How many feet can you bore daily?
Under perfect conditions and depending on the equipment used, you can expect and experienced driller to install 400 - 1000 ft of pipe per day.
6. What is the advantage of directional boring?
The advantage of using horizontal boring include minimal impact to the surface area, extremely strong and durable pipes, quick installation and affordable installation costs.
​
7. How much does directional boring cost?
Each job is unique with it's own below surface or ground challenges. Moreover, the cost of a job also varies with the choice of directional boring contractors. Please enquire for an estimate from a team of experienced professionals who have laid millions of feet of pipe across the US.
BEST DIRECTIONAL BORING EQUIPMENT
At BoringAmericans we use the very best late-model equipment from DitchWitch and Vermeer.

​
Innovation of Ditch Witch machines started in the 1940s when a compact trenching machine was created to replace the pick and shovel for installation of underground residential utility services.
Today DitchWitch offers a wide variety of directional boring machines to cover almost any size job.

VERMEER​
​
In 1943, Gary Vermeer created a mechanical hoist to ease the process of unloading his grain wagon during harvest.
Today, Vermeer holds several product and design patents within its line of utility and track trenchers, directional boring systems and much more.
DIRECTIONAL BORING IN DETAIL
Although they are frequently used interchangeably, the terms Directional Boring and Horizontal Directional Drilling are different because they convey different scales.
Directional or horizontal directional drilling is also used for utility pipe and conduit installations. Horizontal directional drilling (HDD) and ad-hoc auger-boring are great trenchless installation options for utility lines and larger-diameter pipes.
Generally, the term Horizontal Directional Drilling (HDD) is intended to describe large/maxi-sized drill rigs, large bores, and traverse distances of thousands of feet.
Directional drilling, also called horizontal-directional drilling (HDD) horizontal-directional drilling (HDD), is a trenchless, minimum-impact technique for installing underground utilities, such as pipes, conduits, or cables, along a pre-determined subsurface route using surface-mounted drill rigs.
As a minimum impact process, directional drilling offers numerous advantages over conventional trench-heavy methods of installing underground utilities.
This process uses a surface-mounted directional-drilling machine to install utilities in an underground route, rather than digging an open trench the entire length of the utility.
This way of installing conduit has a number of benefits including fewer interruptions of business operations, fewer disruptions to transportation, fewer rehabilitations to land, and directional drilling can also be used to avoid damaging wetlands, streams, and river crossings. Because much of the work is done underground, this also cuts down on the number of permits needed, meaning that your directional drilling company can complete work quickly, with few delays during the process.
Directional drilling is just one more way that ClearPath shows the ClearPath promise of leaving minimal damage on the surface while offering the full spectrum of utility services below ground. Horizontal drilling is used for laying down underground infrastructure.
Next, the drill is brought back above ground, a whirlpool is pulled, then the drilling continues, with the bore changing paths.
Once a gauge confirms the bit is pointed the correct way, the drill string starts turning again. From the surface, the electromagnetic sensors also can monitor the drill bits progress.
Once the drilling process begins, the electrical transmitter (located just beyond the drill bit) transmits a signal back to the operator, who then makes sure that the drill is continuing on the planned route, and is able to make course corrections if necessary.
A spinning drill rod, fitted with a reaming attachment, is then used to make small-diameter pilot holes down the route from a starting point to the finish.
Next, the small diameter pilot hole is increased by boring the drill pipe back and forth through the line using a larger bit attachment, until sufficient room is created for utility installations.
Then, a what-size tube is connected to a reverse-flow drill bit and pulled to the drill bit. During this process, reamer drags a pipeline that is fed drill fluids behind it, preventing it from collapsing.
Unlike HDD drilling, which drags a product back in place, an auger-boring machine moves casings down a hole while drilling, with no need for drilling fluid.
According to Tod Michael, Vermeer trenchless product manager, and Dave Gusmovic, Vermeer MV Solutions Inc. business development manager, horizontal directional drilling and auger boring compliment one another in the context of larger-diameter drilling projects.
The trench-versus-directional-boring cost is typically lower, ranging from six to eight times lower than horizontal drilling.
For larger diameter bores, equipment requirements beyond the HDD are necessary: drilling fluid mixing systems, mud recovery/reclamation systems, diggers for handling drill bits, etc.
Thanks to strong tracing technologies and all of the different types of instrumentation options available to drilling rigs, there are very few conditions in which HDDs cannot be used.
Directional drilling and HDD are similar to the oil-industry-related directional drilling in certain aspects, however, no fair comparisons can be made because the procedures perform significantly different functions.
In the oil and gas industry, directional drilling involves the horizontal drilling of a variety of wells across an area of oil- or gas-bearing rock, angled away from a vertical borehole.
Directional drilling is used mostly for making cross-cuts beneath rivers, roads, and existing structures, for the purpose of installing pipes and pipelines for the transportation of different types of fluids and materials.
Directional boring is used to install infrastructure, such as telecom and electric wire conduits, water lines, sewage lines, gas lines, petroleum lines, product pipelines, and environmental reclamation casings.
A directional boring machine is designed to withstand the unique stresses associated with horizontal drilling for distances from a few yards up to a few hundred yards, as required.
An experienced directional boring team can steer and guide a directional drilling bit up, down, right, left, and combinations of various degrees of each, in order to bore a desired horizontal drilling path.
Unlike conventional utility underground installations, which involve massive trenching -- sometimes for extended periods of time -- directional drilling allows for that to be avoided and to leave the surface relatively unharmed.
Drilling deeper, or at longer distances, and particularly changing directions, presents several extra engineering challenges and stresses to the equipment.
This can mean requiring an entirely new set of equipment, and the new well may have to be drilled again, slightly different in direction.
Cited Sources
​
-
https://www.familyhandyman.com/list/basics-of-horizontal-boring/
-
https://trenchlesstechnology.com/horizontal-directional-drilling-vs-auger-boring/
-
https://www.directionaldrilling.com/Services/Directional-Drilling-Boring/
-
https://www.drillguide.com/en/horizontal-directional-drilling
-
https://drillers.com/directional-drilling-everything-you-ever-wanted-to-know/